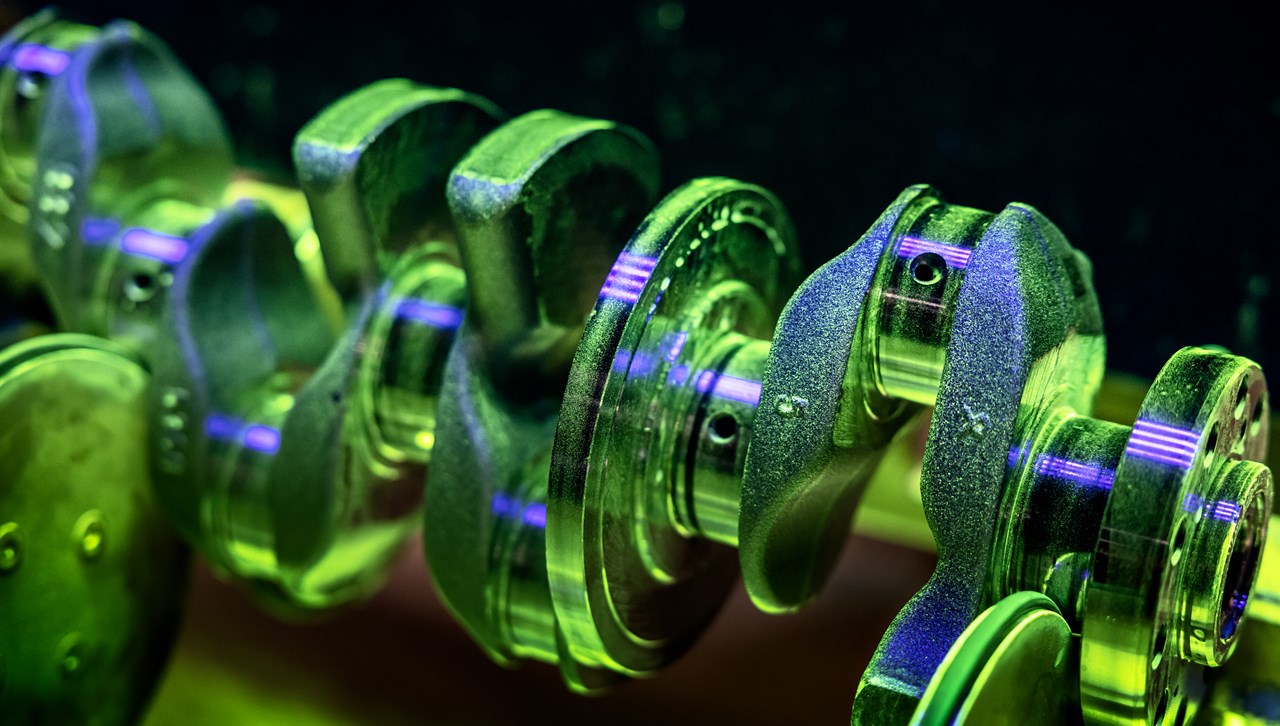
Japansk filosofi vässade motorfabriken
Lean går ut på att få med sig medarbetarna, jobba smartare, effektivisera flöden. Motortillverkaren Aurobay är bland de bästa i Sverige och en avdelning tog sig till final i Svenska Leanpriset – hur kom de så långt?
Det slamrar och pyser med jämna intervaller när vevaxlar till Volvos personbilar förädlas på fabriken i Skövde. Mellan maskinerna står tavlor med detaljerad information om allt som rör jobbet. På vardera sida om gången står höga stolpar med färgade lampor på toppen. Operatörer hastar förbi utan att ge dem någon större uppmärksamhet. Förr spelade ljusfyrarna en huvudroll. Vi återkommer till det.
Det mesta såg annorlunda ut 2018. Då gick startskottet för en transformationsresa på Volvo personvagnars motorfabrik, som numera går under varumärket Aurobay. Grunden är teorierna kring lean, som utgår från Toyotas principer och arbetssätt.
Först ut var avdelningen som bearbetar vevaxlar, en av motorns många detaljer. Snart kom informationstavlorna ut på verkstadsgolvet.
– En del av filosofierna och teorierna går ut på att visualisera. Mycket material hamnade i våra datorer på kontoret förut. Nu vill vi ha det här ute, så att medarbetarna vet vad som händer, säger verksamhetsutvecklaren Patric Nilsson.
Starkt förenklat handlar lean om att ständigt förbättra sin verksamhet. Kärnan är ett fokus på processer och flödeseffektivitet, som i sin tur leder till resurseffektivitet – och pengar att tjäna.
– Man kan lätt gå bort sig utan leanteorierna. Man måste ha flödeseffektiviteten först. Vi har satt människorna i centrum och försökt optimera allt.
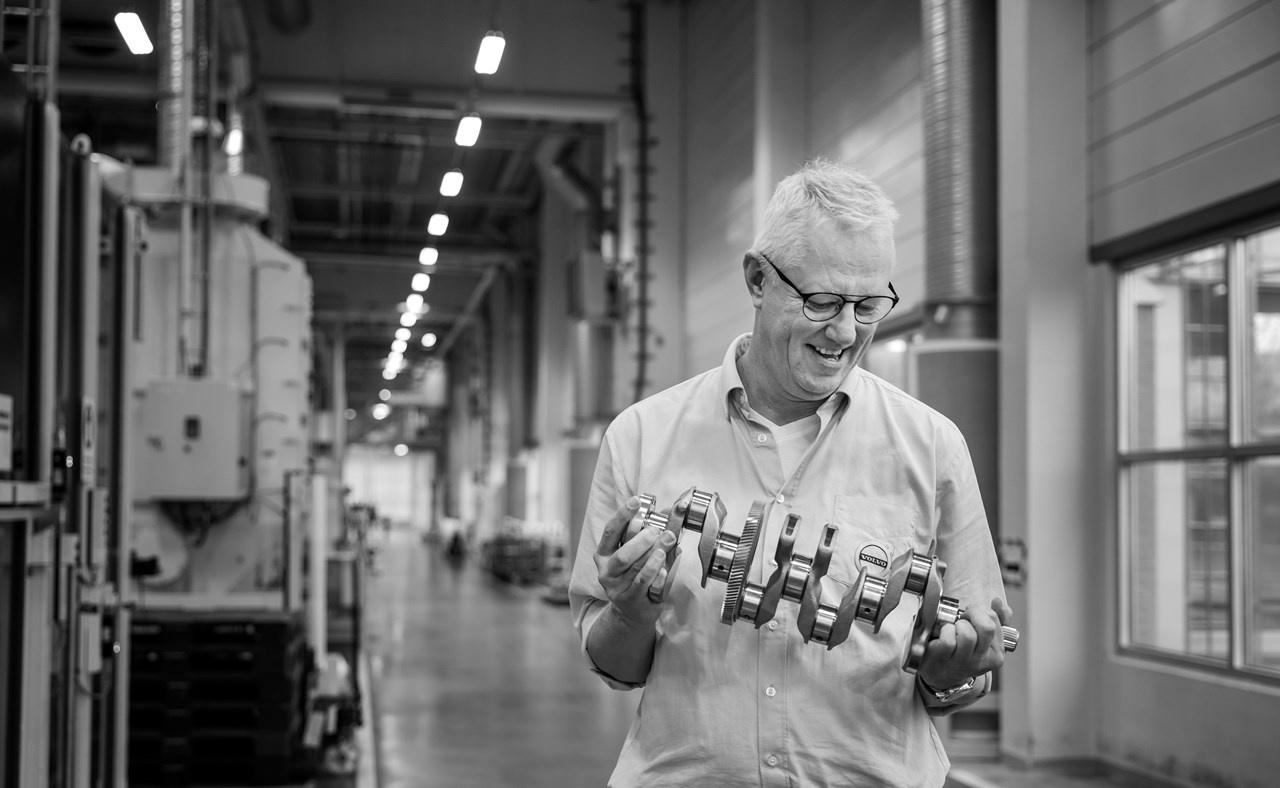
Patric Nilsson pekar ut mot raden av färgade lampor i gången. Här har den stora revolutionen skett. Förr arbetade operatörerna med så kallad line guarding, med ständigt fokus på ljusfyrarna. Blinkande lampor var en signal om att maskiner behövde service, byte av verktyg eller annat. En viktig uppgift, som förhindrade stopp i produktionen. Men ingen visste när lampan skulle blinka. Jobbet gick inte att planera. Maskinen bestämde över människan.
– Line guarding är som att sitta i ett jakttorn och vänta på att älgen ska komma innan man kan skjuta. Vi försökt vända på det, få kontroll över produktionen.
Maskinerna var utrustade med mängder av räknare som talade om när något behövde åtgärdas. De plockades bort. Samtidigt drogs ljusfyrarna ur rampljuset och ett nytt nav med all nödvändig information byggdes upp. Nu går det att planera uppgifterna. Människan bestämmer över maskinen.
– Samtidigt fick vi loss en massa tid, som vi kunnat investera i medarbetarna. Det har gjort linen effektivare. Allt hänger ihop i den här resan, säger Patric Nilsson.
I navet har en lagledare koll på alla zoner och jobb och gör ett schema till varje operatör. Allt från verktygsbyten i maskinparken till tömning av soptunnor planeras in.
Skiftledaren Jonas Andersson sveper med handen över tavlor med kolumner, rader, pilar, siffror … All den informationen fanns i lysfyrarna innan.
– Det här är hjärtat i den dagliga körningen, där vi planerar alla våra aktiviteter. Vi har specat ner varje zon till en viss maskingruppering och vet exakt vad som behöver göras, hur ofta och hur lång tid varje jobb tar. Vi jobbar förutsägbart.
Hur var det förut?
– Ibland hände ingenting och ibland så mycket att man knappt hann med. Det blev aldrig någon bra balans. Nu vet alla vad som ska göras hela dagen. Vi ser också i schemat om operatören har tid att göra kortare uppdrag.
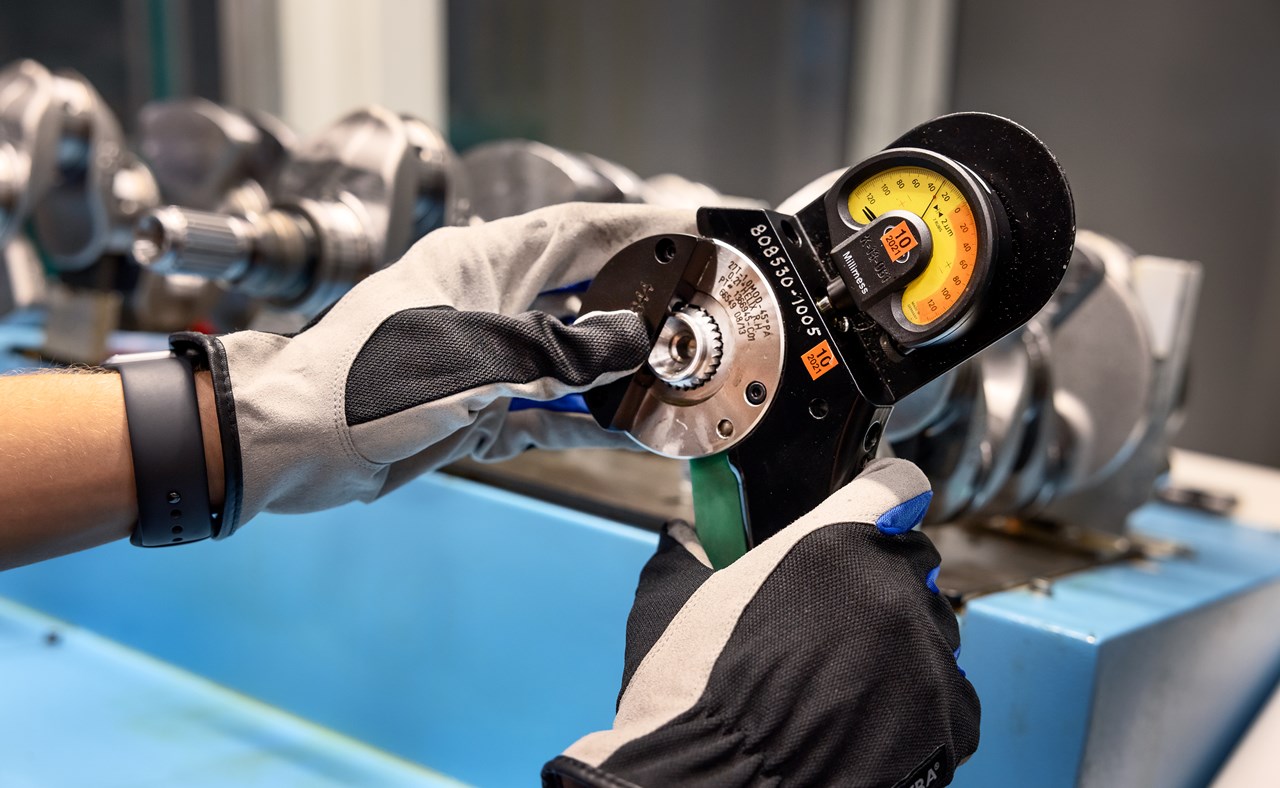
I dag är ett stort antal företag och organisationer engagerade i lean. Föreningen Lean Forum samlar dem på årliga konferenser. Patric Nilsson och en handfull kolleger har varit med i många år. Flera idéer till omvandlingen föddes där.
– Vi använder bilder från Lean Forum när vi ska sälja in förändringarna och få med oss medarbetarna. Vi har handgripligen fått hjälp av föreläsningarna.
Nu vill han inte bara lyssna på andra, utan också bidra. I våras skickade avdelningen in en ansökan till Svenska Leanpriset. Som en av fyra finalister fick de nyligen berätta om sin resa på konferensen.
– Vi vill ha ett starkt industrisverige, som producerar saker och gör tjänster mer effektiva. Då vill vi gärna dela med oss av våra erfarenheter till andra företag.
Anette Kinde är vice ordförande i Lean Forum. Hon är också personen bakom Svenska Leanpriset som föreningen delat ut sedan 2008.
– Syftet är att lyfta förebilder och sprida kunskap om ett arbetssätt som har visat sig ge utmärkta resultat. Från början var mest verkstadsindustrin engagerad. Nu får vi ansökningar från alla möjliga branscher. Det är roligt!
Priset utgår från leanmodellen i boken The Toyota Way, med en helhetssyn som bygger på Toyotas 14 principer. Lean Forum bedömer tävlingsansökningar utifrån tre kriterier: hur organisationen arbetar leant, vilken effekt det har gett och vad andra kan lära.
Styrelsen besökte finalisterna i september, främst för att se verksamheten i vardagen.
– I lean pratar man om Go to Gemba: att gå dit det händer. Man kan inte bara titta på Powerpoints och läsa rapporter, utan måste även se hur det fungerar i verkligheten.
Vad innebär priset?
– Man får ära och uppmärksamhet, mer än något annat. Och stolthet inom företaget, vinnaren är bäst på lean i år, säger Anette Kinde.
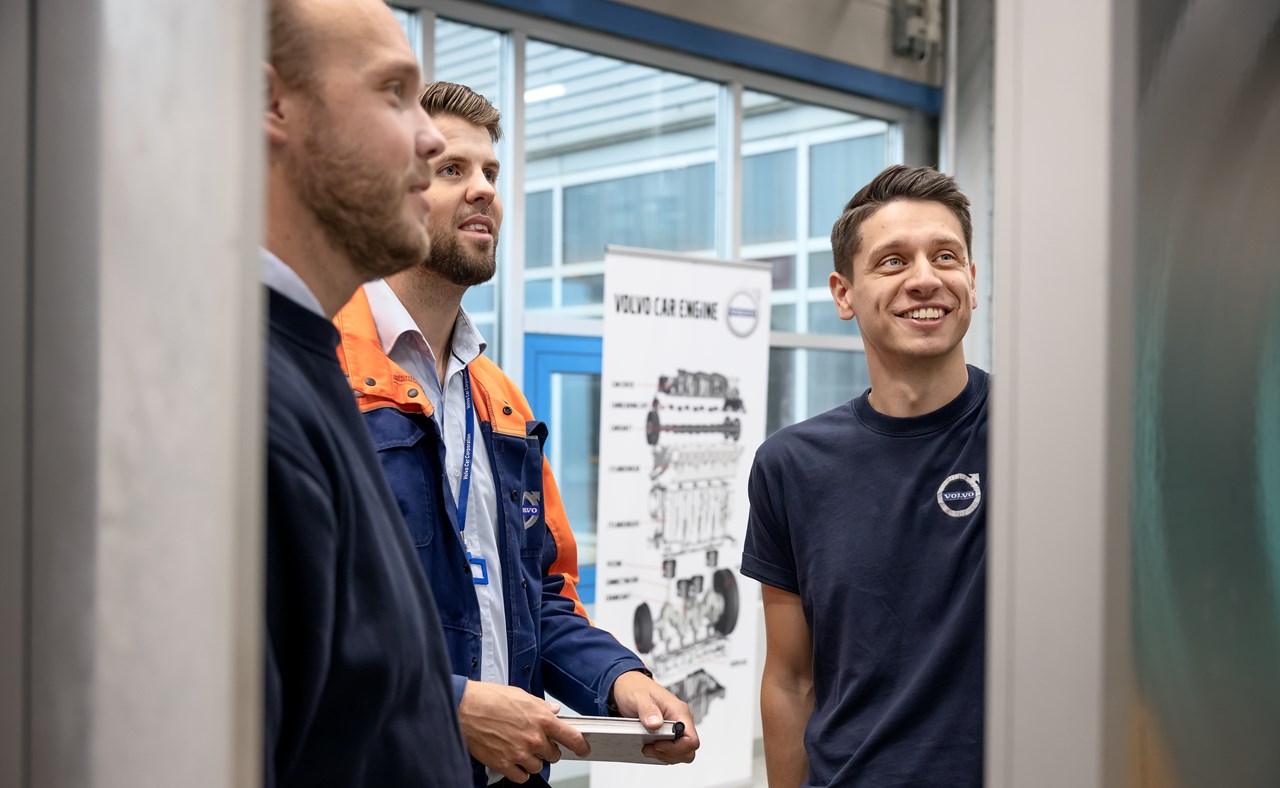
På avdelningen vevaxlar arbetar ett 30-tal personer fördelade på tre skift. En av dem är Alvedin Dindic. Han har jobbat på olika delar av företaget sedan studenten från Volvogymnasiet 2014. Nu är han ”predictable-operatör” och utför uppgifter enligt dagsschemat. Däremellan ägnar han sig bland annat åt aktiviteter kring ständiga förbättringar.
Han kom in i avdelningens förändringsresa 2020. Schemat med de tydliga hållpunkterna är den stora skillnaden.
– Jag vet exakt när jag ska göra ett jobb och vad och kan planera in de extrajobb jag ska göra under dagen. Det blir ju lugnare.
En annan skillnad är arbetsinstruktionerna. Tidigare skrevs de av supportfunktioner, ur en ingenjörssynpunkt. Det blev ofta ett glapp mellan teorin och hur människor faktiskt jobbar. När operatörerna slapp punktbevaka lampor fick de tid att jobba med förbättringsarbeten och fundera ut hur de egentligen borde göra sitt jobb.
Alvedin Dindic har bidragit till gruppens arbetsinstruktioner. Han har också varit med och sett till att avdelningen fått ansvar för nya uppgifter.
– Förr kom personal från en annan avdelning för att ta prov på våra tvättvätskor. Nu gör vi det själva i stället. Vi tog fram förslaget gemensamt i en grupp och det gick igenom.
Varför ville ni ta över det jobbet?
– Enligt det arbetssätt vi har nu ska produktionen ta hand om så mycket som möjligt själv. Förr lejde man bort allt hela tiden och bara koncentrerade sig på line. Nu tar vi mer kontroll och använder inte kringorganisationer lika mycket.
En tredje skillnad är större arbetsrotation. I stället för att dela upp uppgifter jobbar operatörerna med alla avdelningens processer.
– Vi går in på områden som vi inte sysslade med förut, får blanda lite och tänka på ett helt annat sätt. Det är spännande och utmanande. Och jobbet blir roligare, säger Alvedin Dindic.
Han känner inte till någon annan som jobbar på samma sätt.
Är det viktigt att tävla i lean?
– Personligen tycker jag att det blir ett annat fokus på själva arbetet med att utveckla ännu bättre och kunna vara med och konkurrera. Bilbranschen är rätt tuff. Man måste var top notch!
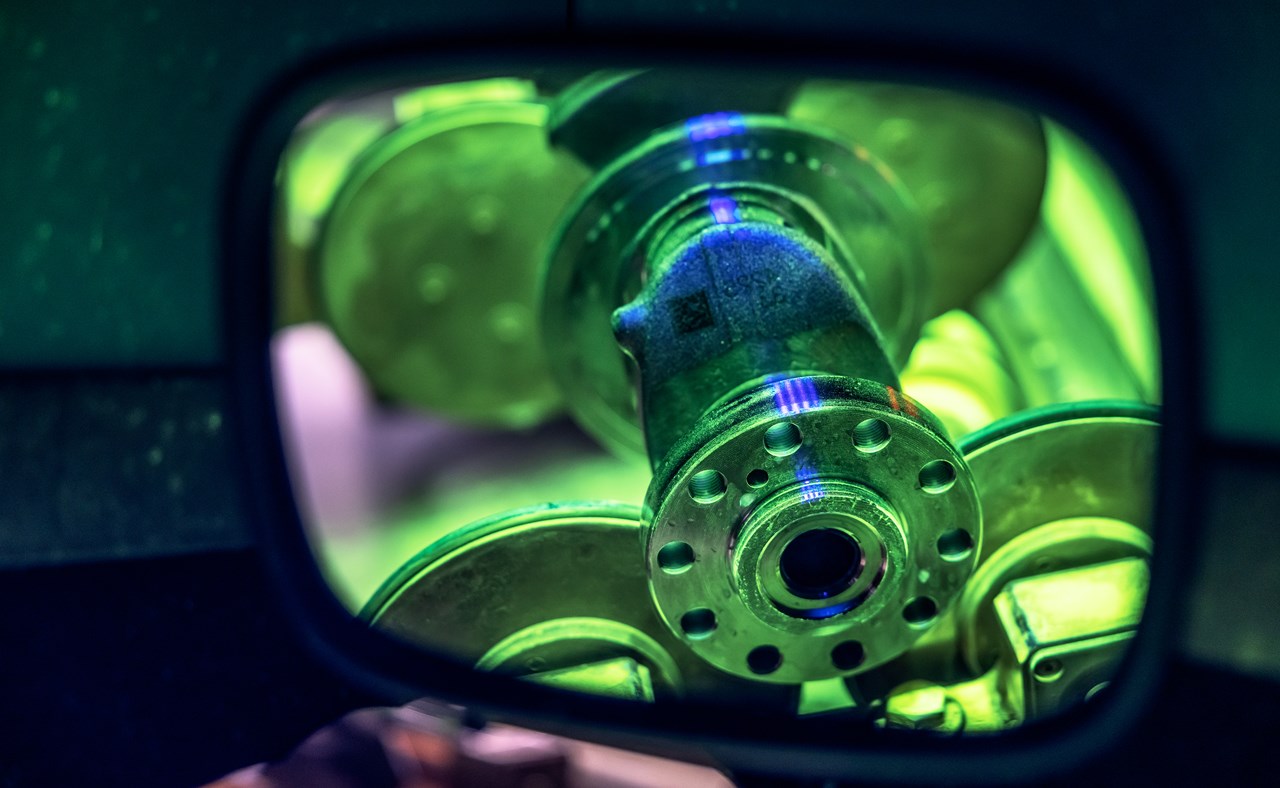
Patric Nilsson tycker att det hade varit roligt att vinna, framför allt för personalen. Men att tävla är inte så viktigt.
– Jag vill att fabriken ska se annorlunda ut i morgon jämfört med igår. Vi kommer aldrig att bli färdiga. Det är bara att fortsätta ta sig an nästa problem, nästa möjlighet. Den resan är viktigast, för den stärker vår konkurrenskraft.
Han räknar medarbetarnas kunskap som en framgångsfaktor. En annan är ledningens driv.
– Allt annat är maskiner och metoder, det kan man påverka om man vill. Och man måste ju vilja ganska mycket. Lean är ingen quick fix.
Enligt Patric Nilsson klev de flesta medarbetarna villigt på förändringståget.
– Jag har inte behövt jobba med att involvera dem. Operatörerna vill förbättra sin vardag och driver sitt eget förbättringsarbete. Vi andra ska guida och coacha.
Men motstånd fanns. Vissa har fortfarande svårt att acceptera arbetssättet och ändra invanda rutiner. Där ser produktverkstadschefen Filip Jerenvik också möjligheter.
– Motståndet utvecklar oss och får oss att tänka steget vidare hela tiden. Operatörerna ställer utmanande frågor om varför vi gör på ett visst sätt. Då måste vi bli ännu tydligare med syftet och mer visuella.
Fabrikens leanresa startade med vevaxlarna, men stannar inte där. Visionen är att transformera hela värdeflödet.
– Nu skapar vi flöde i fabriken och sprider de metoder och arbetssätt vi utvecklat. Vi vill sedan bygga ett flöde ändå från våra leverantörer till våra kunder. Det kommer förhoppningsvis att stärka leverantörerna, som jobbar på samma resa, och är i bästa fall också bra för kunden, säger Patric Nilsson.
Vilka effekter ser ni?
– Vi påverkar många olika saker. Medarbetarna utvecklas varje dag, våra resultat blir bättre. Den största effekten är på flödeseffektiviteten. Bilbranschen är konkurrensutsatt så vi måste verkligen jobba med vår konkurrenskraft.
Hur kan andra företag lyckas med lean?
– Börja med ledningen, den måste se vinsten och vad man kan få ut. Och man måste ha ett brinnande intresse för att verkligen fördjupa sig. Det går inte att bara göra en del. Många saker hör ihop, lean är ett helt pussel.
Text
Minna UlinFoto
Sofia Sabel