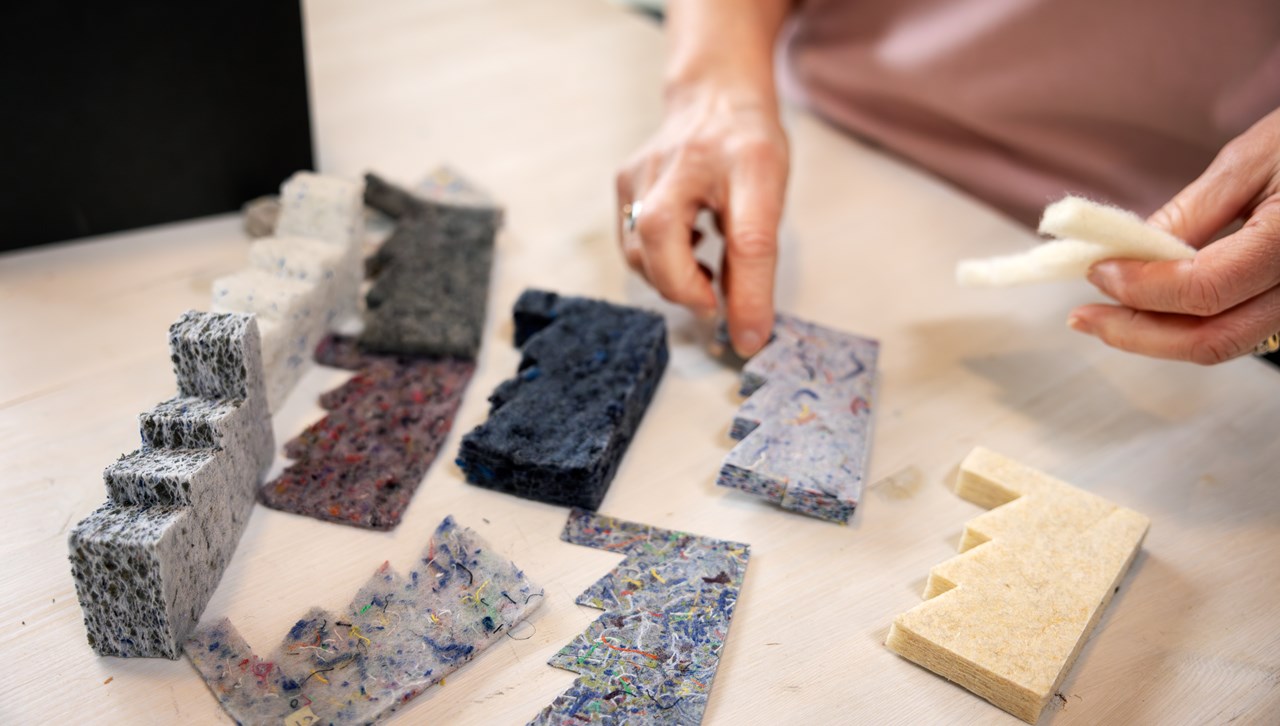
Ny revolutionerande teknik för mer hållbara förpackningar
I Varberg driver The Loop Factory och Yangi utvecklingen av fiberbaserade material med en teknik som kan revolutionera förpackningsindustrin. Genom att ersätta traditionell tillverkning med en torrformningsprocess minskar vattenförbrukningen och energianvändningen rejält – samtidigt som produktionen blir snabbare och billigare.
– Det finns en jättestor potential att växa inom förpackningsindustrin, säger Johann Kaiser, vd på Yangi.
Fram till 2021 var Yangi en del av The Loop Factory som arbetar med utvecklingsprojekt inom fiberbaserade material. Tillsammans insåg de att det krävdes mer utvecklingsarbete med maskiner för torrformning av cellulosa och därför tog Yangi in externa investerare, bland annat industrikoncernen Voith och modehuset Chanel.
Även om Yangi och The Loop Factory numera inte är inom samma bolag har de en gemensam teknikplattform för att skapa fiberbaserade material med en torr process. De samarbetar också genom att dela kunskap, personal och lokaler. Totalt jobbar 40 personer i bolagen.
– Trenderna går mot mer hållbarhet och många stora bolag har sagt att de ska ersätta alla sina plastförpackningar med mer miljövänliga och återvunna förpackningar. Det kommer också successivt mycket ny lagstiftning kring förpackningar för att minska plastanvändning och att hitta alternativ till engångsplast. Det handlar om en mångmiljardmarknad, säger Johann Kaiser.
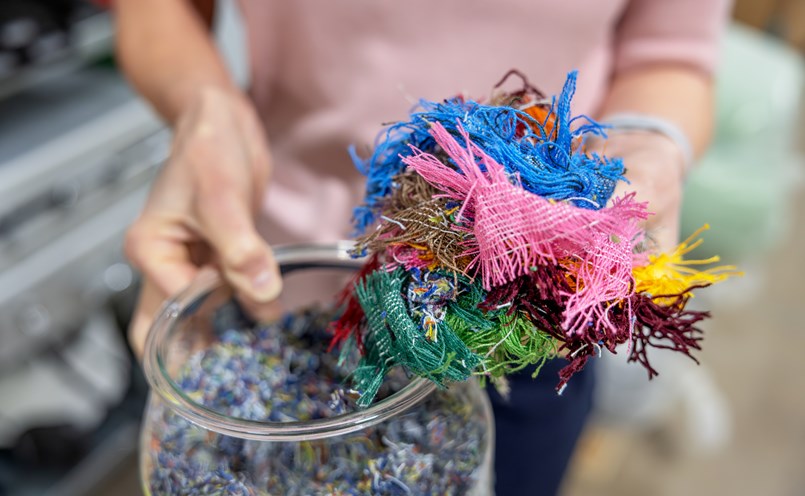
För att kunna ersätta plast behövs andra material som finns i stora volymer och där är pappersfibern ett bra alternativ. Råvaror för att tillverka papper finns i stora mängder liksom uppbyggda leverantörskedjor. Det producentansvar som finns har dessutom resulterat i rutiner för att återvinna papper.
Den vanligaste tekniken för att tillverka pappersförpackningar är genom våtformning. Den innebär att nya eller återvunna fibrer behandlas med vatten och kemikalier för att separera fibrerna. I nästa steg pressas och torkas pappersmassan. Processen kräver både mycket vatten och energi. På Yangi använder man i stället en luftbaserad teknik tillsammans med 3D-torrformning. Cellulosan bryts upp mekaniskt i en kvarn, sedan blandas den med luft och sist formas och pressas materialet till olika förpackningar. Detta innebär att man inte behöver något processvatten och tillverkningen kräver dessutom betydligt mindre energi. Enligt bolaget så minskar koldioxidutsläppen från tillverkningen med 70 procent.
– Vår teknik har stora miljöfördelar och lägre produktionskostnader eftersom vi använder mindre energi och vatten. Dessutom går det snabbare att tillverka förpackningarna än vid våtformning. Däremot kan vi inte göra lika många slags former som vid traditionell tillverkning, men det är något vi jobbar mycket med, säger Johann Kaiser.
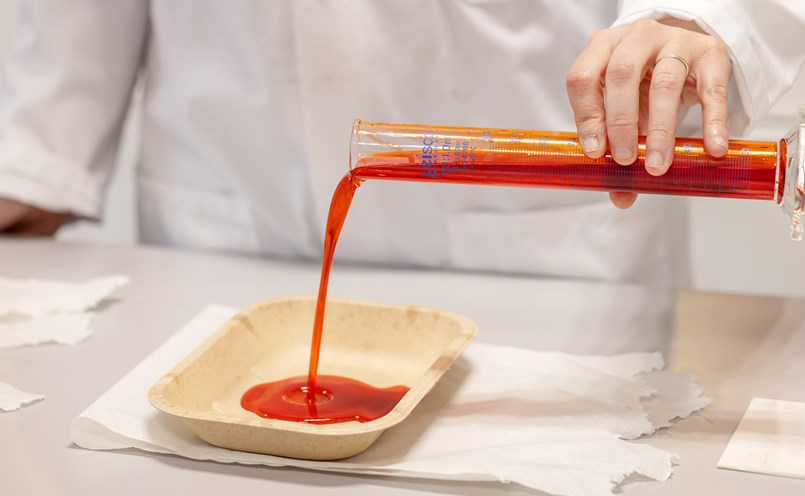
I dagsläget använder Yangi nya fibrer, men tanken är att framöver även nyttja återvunnen fiber i tillverkningen.
– Vi vill få förpackningstillverkare att använda vår teknik så fort som möjligt. Då behöver de maskiner, material, recept och verktyg. Det vi tillhandahåller är en helhetslösning, så när kunden har köpt vår maskinteknik är den redo att producera förpackningar, säger Johann Kaiser och förklarar att den stora utmaningen är att komma med en ny teknik till marknaden.
– Ofta har man använt samma teknik under väldigt lång tid. Men redan nu säljer vi till kunder i hela världen och jag tror vi i framtiden kan att bli ett nytt Tetra Pak, säger Johann Kaiser
Vad har då hänt med The Loop Factory sedan avknoppningen av Yangi?
– Vi har byggt upp bolaget på nytt och gått från fyra till tio anställda. Vi har fortsatt att arbeta med utvecklingsprojekt kring fiberbaserade material och då i första hand återvunna material. Där är vår teknik och arbetsprocess lämpliga, säger Maria Ström, vd på The Loop Factory.
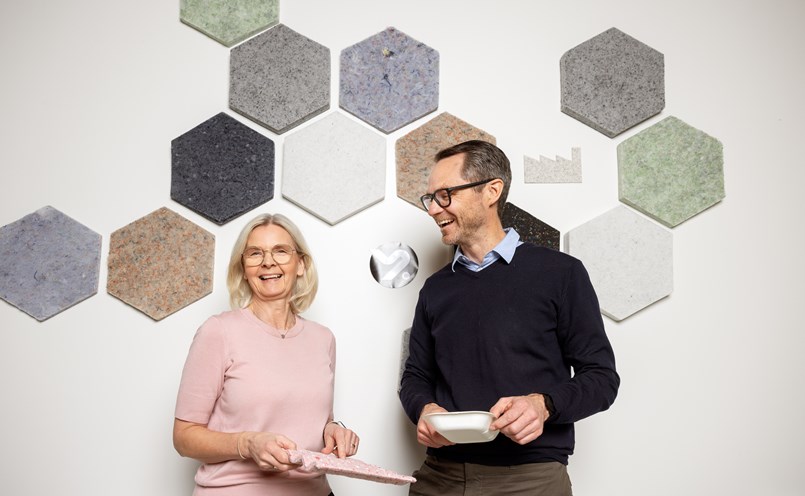
Vilka material det handlar om beror på kunden. Extra aktuellt är textilåtervinning med anledning av en ny lag som trädde i kraft den 1 januari 2025. Den innebär att all textil inom EU ska samlas in separat för återvinning och återbruk.
– Det betyder att företag ska ha en plan för sina textila restströmmar och att producenter som har spillmaterial ska få in det i sina system. För oss är det positivt att det finns ett stort intresse kring textiler just nu, säger Maria Ström.
En utmaning är att många kunder inte brukar utveckla material, utan köper en hel kollektion, vilket är vanligt inom exempelvis klädindustrin.
– Det är en process att få dessa aktörer att förstå att det kostar att utveckla material och det kommer att krävas mycket samarbete för att lyckas med detta, säger Maria Ström.
Själva utvecklingsarbetet kan exempelvis handla om kunder som vill bli cirkulära och behöver hjälp med vad de kan göra med sitt spill.
– Vi brukar fråga var bolaget vill vara framöver, hur deras strategiska plan ser ut, och om ett material utvecklat av återvunnen råvara kan bli en del av kundens framtid. Vi tar sedan fram prototyper i vårt labb och planerar redan från början att det ska gå att skala upp och ha materialet i produktion. Det stärker möjligheterna att få ut återvunna material på marknaden, säger Maria Ström.
Text
Ann-Sofie BorglundFoto
Sofia Sabel